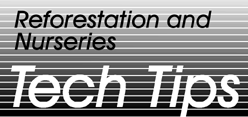
Mary Ann Davies and Ted Etter, Project Leaders
Figure 1—Overhead irrigation is often used to water plants in nurseries.
Highlights...
- When native plants are grown in containers,
overhead irrigation may not be effective
because the plants' large canopies may
intercept much of the water.
- Subirrigation (watering container plants
from the bottom up) would be an attractive
alternative if watering could be automated,
as it is for overhead irrigation systems
- The Missoula Technology and Development
Center developed an automated system that
waters container plants from the bottom up
when the potting soil dries out.
- This tech tip includes information on assembling and operating an automated system for subirrigating container plants in a nursery.
Native plants grown for restoration projects on national forests are usually started in containers. Forest Service nurseries use overhead irrigation for the container plants because it's inexpensive and relatively simple (figure 1). Overhead irrigation becomes less effective when plants have large canopies that may intercept the water. This is often the case with native plants. To compensate, more overhead irrigation must be applied, which wastes water and has the potential to carry fertilizer (especially nitrates and phosphates) into surface water and groundwater.
Subirrigation is a different approach that waters from the bottom up. This technique relies on the capillary action of potting soil to draw water from a reservoir tray into the containers. Subirrigation can use water more efficiently, reducing fertilizer runoff and watering plants more evenly and accurately. One problem with subirrigation is that employees have to turn the water on and off for each watering. Because employees aren't always available, the plants may dry out and die.
The Forest Service nursery in Moscow, ID, is testing subirrigation for native plants. Researchers proposed that the Missoula Technology and Development Center (MTDC) develop a system to automatically regulate watering intervals based on the moisture content in the potting soil.
The nursery has a 75-gallon water tank beneath the growing bench (figure 2). A submersible pump, wired to a programmable, electronic timer, sits in the water tank. Based on estimates of when the plants might need irrigation, the timer turns the pump on just long enough to fully flood the tray. The tray takes about 20 minutes to drain. The cycle may have to be repeated until the soil reaches the appropriate moisture content.
MTDC designed an automated subirrigation system that includes a soil moisture sensor, a drain assembly, and a controller (figure 3). The controller is set for specific voltages, representing dry and wet soil moisture levels based on the plant's needs. The soil moisture sensor monitors the water content in the soil. If the soil is too dry, the controller activates the pump. The controller activates the solenoid drain valve before the soil becomes too moist.
Figure 2—The nursery in Moscow, ID, uses a 75-gallon water tank,
submersible pump,
and programmable timer for subirrigation.
Figure 3—MTDC designed an automated subirrigation system that
includes a soil moisture sensor, a drain assembly, and a controller.
The soil moisture sensor, an ECH2O EC-5 manufactured by Decagon Devices, Inc., is inserted into the soil in one of the container plants (figure 4), ideally one of the last to receive water when the tray is filling. The container with the sensor can be up to 15 feet from the controller.
Figure 4—An ECH2O EC-5 soil moisture sensor, manufactured by
Decagon Devices, Inc. (inset),
is inserted into the potting soil in one of the
container plants.
The drain assembly includes a solenoid valve, a backflow valve, a water feed nozzle, and additional pipe fittings that connect the water pump hose and drain outlet to the water tank (figure 5). The water feed nozzle attaches the drain assembly to the irrigation tray. The water pump hose connects to the backflow valve side of the assembly. The backflow valve lets water flow into the irrigation tray when the pump is activated, but will not let water flow back into the pump when the pump is turned off. The solenoid valve opens when it is activated by the controller, allowing water in the irrigation tray to drain back into the water tank.
Figure 5—The drain assembly includes a solenoid valve,
a backflow valve, a water feed nozzle, and additional
nylon pipe fittings.
Because the irrigation trays typically are made from lightweight plastic and the backflow valve and solenoid are both heavy brass fittings, nylon pipe fittings were used to reduce the weight hanging from the irrigation tray. A thin stainless steel plate in the tray helps distribute the weight (figure 6). To prevent leaks, Teflon tape was used on all connections and a butyl rubber gasket was used under the water feed nozzle where it attaches to the irrigation tray.
Figure 6—A thin stainless steel plate under the water feed nozzle helps
distribute the weight of the heavy brass fittings.
The 120-volt controller (figure 7) lets the user set the dry and wet soil moisture voltages. The dry soil moisture voltage activates the water pump and the wet soil moisture voltage activates the solenoid drain valve. The controller also lets the user determine how long to run the water pump and how long to keep the drain valve open.
Figure 7—The automated subirrigation controller.
Controller Settings
Before setting the wet and dry soil voltages, the user should use a voltmeter to measure the voltage coming from the soil moisture sensor for potting soil that ranges from very dry to very wet (saturated). Start with very dry soil (figures 8 and 9) and add a little water then, record the voltage until the soil is very wet. Add 25 millivolts to the measured voltage of very dry soil and subtract 25 millivolts from the measured voltage of very wet soil to account for electrical noise.
Figure 8—The user sets the dry soil moisture voltage so the controller will
activate
the water pump
(probe connections shown) and sets the wet soil
moisture voltage
so the controller will activate the drain valve before the
soil becomes too moist.
Figure 9—This example shows that the voltage indicated by
a soil
moisture
sensor in soil increases as potting soil becomes moister. Dry soil may
have
a voltage
of 900 millivolts (activation voltage would be set to 925 millivolts
in this example to account for electrical noise). When the potting soil is
completely
saturated,
the voltage will be 2,200 millivolts (the drain activation
voltage would
be set to 2,175 millivolts to account for electrical noise).
Controller Operation
The water pump's operating time can be programmed in 18-second intervals up to a maximum of 30 minutes. The pump should run long enough to fill the irrigation tray with enough water for all the containers. The drain valve can be programmed to open for 9 or 18 minutes. Every 38 minutes, the drain valve opens for 20 seconds to drain off any water that might have seeped out of the containers.
MaterialsPart | Supplier | Part No. | Cost |
---|---|---|---|
1-inch NPT zero pressure solenoid valve | McMaster-Carr | 4711K953 | 160.14 |
¾-inch NPT brass threaded tee | McMaster-Carr | 4429K254 | 8.18 |
1-inch NPT female Buna-S brass piston check valve | McMaster-Carr | 7746K83 | 37.99 |
¾-inch brass hollow hex head plug | McMaster-Carr | 59785K521 | 8.27 |
1⁄8- by ½- by ½-inch Buna-N rubber sheet | McMaster-Carr | 8635K564 | 5.95 |
¾-inch nylon 90-degree elbow | Dultmeier | TW SE34 | 2.59 |
1- by ¾-inch nylon bushing | Dultmeier | TW RB10-34 | 1.62 |
¾-inch MPT by ¾-inch barb pipe-to-hose nylon fitting | Dultmeier | TW A3434 | 0.52 |
¾-inch nylon hex nipple | Dultmeier | TW M3400 | 0.50 |
Suppliers
Dultmeier Sales
P.O. Box 45565
Omaha, NE 69145–0565
Phone: 888–677–5054
http://www.dultmeier.com
McMaster-Carr
P.O. Box 54960
Los Angeles, CA 90054–0960
Phone: 562–463–4277
http://www.mcmaster.com
Anyone interested in building a subirrigation controller can call Ted Etter (406–329–3980) at MTDC to request electronic drawings. In the future, Decagon Devices, Inc., may start building controllers for their soil moisture sensors if customers express enough interest.
AcknowledgmentsMTDC would like to thank Kas Dumroese, Anthony Davis, Jeremy Pinto, and the nursery technicians at the Moscow nursery for testing the controller and helping us refine it until it met their needs.
About the AuthorsMary Ann Davies received a bachelor's degree in mechanical engineering with a minor in industrial and management engineering from Montana State University. She worked in the Pacific Northwest Region as a facility engineer and as a tramway engineer. Davies has worked in fire management as a crewmember and as a crewboss. She worked for 5 years with the Rocky Mountain Research Station in the fire chemistry and fire behavior groups before coming to MTDC in 1999.
Ted Etter joined MTDC in 2002 as an electronics engineer and project leader. He has 20 years of experience working for private industry in the design of test equipment, display devices, and medical instrumentation. In the 6 years before he joined MTDC, he taught courses in the electronics technology program at the University of Montana College of Technology, Missoula. His work at MTDC includes projects in wireless communications, alternative energy sources, instrumentation, and process control. Etter has a bachelor's degree in mathematics from the University of Oregon and a master's degree in teacher education from Eastern Oregon State University.
For additional information about subirrigation controllers, contact MTDC:
USDA Forest Service
Missoula Technology and Development Center
5785 Hwy. 10 West
Missoula, MT 59808-9361
Phone: 406-329-3900
Fax: 406–329–3719
Forest Service and Bureau of Land Management employees can search a more complete collection of MTDC's documents, CDs, DVDs, and videos on their internal computer networks at:
http://fsweb.mtdc.wo.fs.fed.us/search/
Electronic copies of MTDC's documents are available on the Internet at: